降低液力耦合器滑差率,有2種方案可供選擇:
1)對給水泵葉輪進行車削,降低給水泵在原有工作轉(zhuǎn)速下的壓頭和流量。當(dāng)需要達(dá)到原有的壓頭和流量情況下,就必須提高給水泵(熱泵)的工作轉(zhuǎn)速,從而達(dá)到降低液力耦合器滑差率的目的。
2)對液力耦合器進行改造,減小液力耦合器增速齒輪的傳動比,這樣就可以降低泵輪轉(zhuǎn)速,使液力耦合器輸出端的轉(zhuǎn)速與給水泵滿負(fù)荷工況下的工作轉(zhuǎn)速接近,從而達(dá)到降低液力耦合器滑差率的目的。
對比以上2種方案,第1種方案投資小,風(fēng)險較低,但計算比較困難。第2種方案投資較大,風(fēng)險較高,但能夠計算出改造后給水泵的運行參數(shù)。經(jīng)過綜合比較,我們終選擇投資較小,風(fēng)險較低的第1種方案,即對給水泵葉輪進行車削。
2改造效果理論測算
采取幾種不同的方法對改造后的給水泵節(jié)能效果進行理論測算。
2.1根據(jù)液力耦合器效率進行計算
1)車削葉輪前液力耦合器效率:
2)車削葉輪后液力耦合器效率:
3)車削葉輪前后功率損失差值
2.2根據(jù)液力耦合器功率損失進行計算
2.3根據(jù)能量平衡的方法進行計算
根據(jù)液力耦合器的理論,其在工作中的功率損失終全部轉(zhuǎn)變?yōu)闊崃浚@些熱量一部分通過液力耦合器的零部件,殼體向周圍散熱,絕大部分加熱了工作液體,使工作液體溫度升高,因此通過測定工作油冷油器和潤滑油冷油器的溫升,就可以知道液力耦合器的功率損失。因為測定油的流量比較困難,通過測量冷卻水的流量來計算其換熱量的大小,也可以間接知道液力耦合器的功率損失。用機組在220MW負(fù)荷下的工況和在190MW負(fù)荷下的工況作對比.
前2種方法計算出的結(jié)果偏小,主要有以下原因:
1)在機組帶同樣的220MW負(fù)荷工況下與機組分別帶220MW,190MW工況時,由于后者液力耦合器的輸入功率下降(220MW大約為4250kW,而190MW時大約為3900kW),在液力耦合器效率同樣下降的情況下,其功率損失值也小些,如果以液力耦合器效率下降4計算,其功率損失值偏小14kW.
2)以上計算沒有考慮通過液力耦合器殼體等部位向外的散熱量。
因此,如果通過葉輪車削,給水泵轉(zhuǎn)速由4650 r/min升至5000r/min,滑差率減少6.6,功率損失應(yīng)該在200kW左右。
實際上,好的方法是通過計算在不同的滑差率下液力耦合器的效率,然后按照其輸入功率計算功率損耗差值。但這種方法需要測定前置泵,給水泵,電機的軸承等部位所產(chǎn)生的摩擦損失,基于現(xiàn)實條件,很難做到,因此采取以上的計算方法來估算還是比較可行的。
比較以上3種計算方法可知,如果能夠知道工作油流量和潤滑油流量,采用能量平衡法比較合適。
幾種方法雖然計算上都有誤差,但通過估算可以預(yù)測出柳電公司給水泵車削葉輪后液力耦合器的功率損失至少可減少約200kW,節(jié)能效果顯著,經(jīng)濟效益非常可觀。
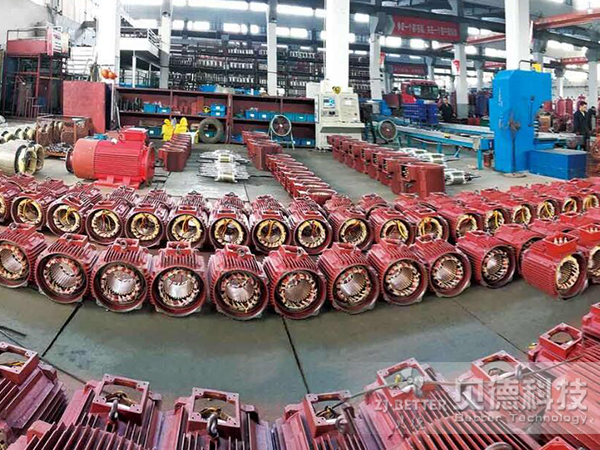